Just a few decades ago, Central Europe was full of active mines that extracted a wide variety of resources. Even smaller deposits were exploited back then, but with increasing globalisation and falling world market prices, many had to close down. Some mines have become museums, others adventure playgrounds. But somewhere in a small valley in Italy, an old fluoride mine has been decaying for the last two decades. Welcome to Miniera T…
Dieser Artikel ist auch auf Deutsch verfügbar. Click here to find out more about Italy!
Caution: This facility is a very dangerous Lost Place! For your own safety, the coordinates are intentionally inaccurate.
History
Exactly when mining began in this small valley on the “Via di Ferro”, the “Iron Road” in the Italian Province of Brescia, is not known. For centuries, anyone was allowed to mine iron ore without further permission. A myriad of shafts were driven into the mountains, some closed again, some collapsed, and others grew together to form entire mines.
Iron was mined in most of the more than 100 known mines in the region. Not so in the Miniera T., where Silver was dug out of the hills starting in the the 15th century. This alone makes the mine quite special. However, the silver vein was probably not very productive at the time. A document from 1718 mentions the reopening of the silver mine due to the discovery of a new vein, suggesting that there must have been a period of inactivity beforehand.
Disastrous floods resulted in only 12 of the region’s 108 mining operations being active by 1752. It is not known whether Miniera T. was among the affected companies. However, silver mining seems to have finally stopped somewhere around this point. Zinc and lead were produced instead, which were extracted from sphalerite (zinc blende) and galena (lead blende), which often occur in the vicinity of silver veins.
The few remaining mines in the valley were consolidated under the umbrella of the Società degli Alti Forni, Acciaierie e Fonderie di Terni in the 19th century. In the 1860s, however, the company could no longer keep up technologically and ceased operations. British The Brescia Mining and Metallurgical Co.Lim. bought up the most promising mines in 1894, including Miniera T., and tried to start over. This attempt also failed. In 1904 there was not a single active mine left in the entire area.
Mining of fluorite, which became increasingly important in the production of glass, ceramics and steel at the beginning of the 20th century, finally breathed new life into Miniera T. After being reopened by the Martelli company, the mine changed hands several times through mergers and acquisitions and seems to have survived the Second World War quite unscathed. The flotation plant erected on a river outside the shafts even received a modern rotary kiln around 1943.
Large orders and loans from the Government of the United States of America drove production to its peak in the 1950s. Between 10 and 12 tons of fluorine were exported to the USA in 1948, raising to 90 tons by 1952. The flotation plant was one of the largest in Europe at that time.
The 1960s were marked by falling demand, falling world market prices and rising production costs. Within just a few years, the owner changed several times, for a short time the mine even belonged to Montecatini Edison S.p.A., one of the largest chemical conglomerates in Europe. But even that could not stop the gradual collapse. In 1979, for example, 74 of the 100 employees were on short-time work. In 1995 the company still had about 30 employees, about half of whom working underground.
In 1999 operations finally closed down for good. Since then, the facilities have fallen into a state of disrepair, but the pictures clearly show that maintenance was neglected long before that.
The flotation plant
The material extracted underground was transported to the surface via several conveyor belts and then crushed, washed, cleaned and sorted according to weight and size.
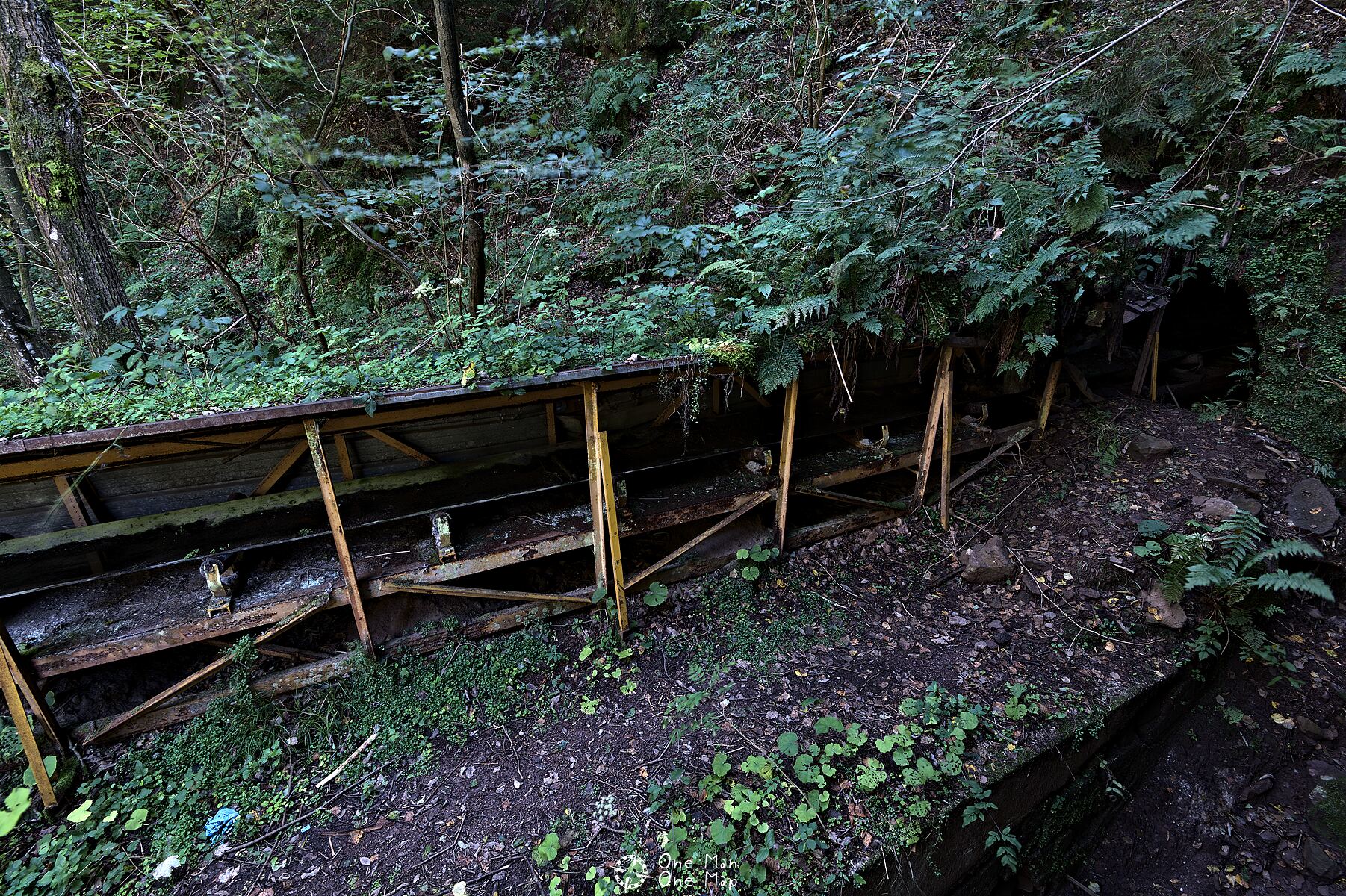
The old mine shafts are accessible via detours, but you should not go there alone under any circumstances! No security measures have been taken for more than 20 years. The few recent photos and videos available show large holes, lots of water and many rotten wooden beams.
In a flotation plant, minerals are separated from each other by various processes as they flow through different implants. For example, centrifugal separators (colloquially refered to as “cyclones”) or chemical processes such as the separation of elements with reaction foams are being used.
At the beginning of the 20th century, such plants were usually built in multi-storey buildings on a slope. We start in the machine room on the third floor.
The entire building is filled with an unmanageable tangle of machines, pumps and pipes. The various mining products such as lead, tin, silver, fluorine and sulfur were separated, enriched and processed on their way through the various cascades. A laboratory monitored the correct composition of the intermediate and end products.
These strange machines here were probably used for separation by foam extraction. This process takes advantage of the different solubility of chemical compounds in liquids. The minerals are dissolved in water and then mixed with a chemical that binds to the desired compound (e.g. silver or lead). The resulting compound repels water and rises to the top of the pool, where it can be skimmed off. This recovers even the smallest leftovers. A similar process is also used in waste water treatment.
To speed up the process and increase efficiency, an agitator (driven by the pulley at the top) creates air bubbles in the liquid. The water-repellent particles stick to the bubbles and create a foam on the surface, which is skimmed off into the collection trough at the front. From there it goes on to the next processing step.
The flotation plant extends to the other side of the river. Two covered bridges connect the annex building with the 1st and 2nd floors of the main building. Together with a small overhead crane, they form a characteristic “Z” that can be seen from afar.
It is not obvious why exactly the tunnels were roofed in such a complex way. The few pipes running here could have been laid without a roof. In fact, there is a whole series of additional cables hanging freely on a steel cable across the river.
The idea that larger amounts of material might have been carried back and forth between buildings by hand also doesn’t seem to make much sense. This can only be done on one of the bridges, the other can only be reached via a thin ladder…
I can only discourage from stepping on the visibly dilapidated bridges. The only thing that stands between your health and a fall into the creek bed a few meters below are old wooden planks and a few rusty metal beams!
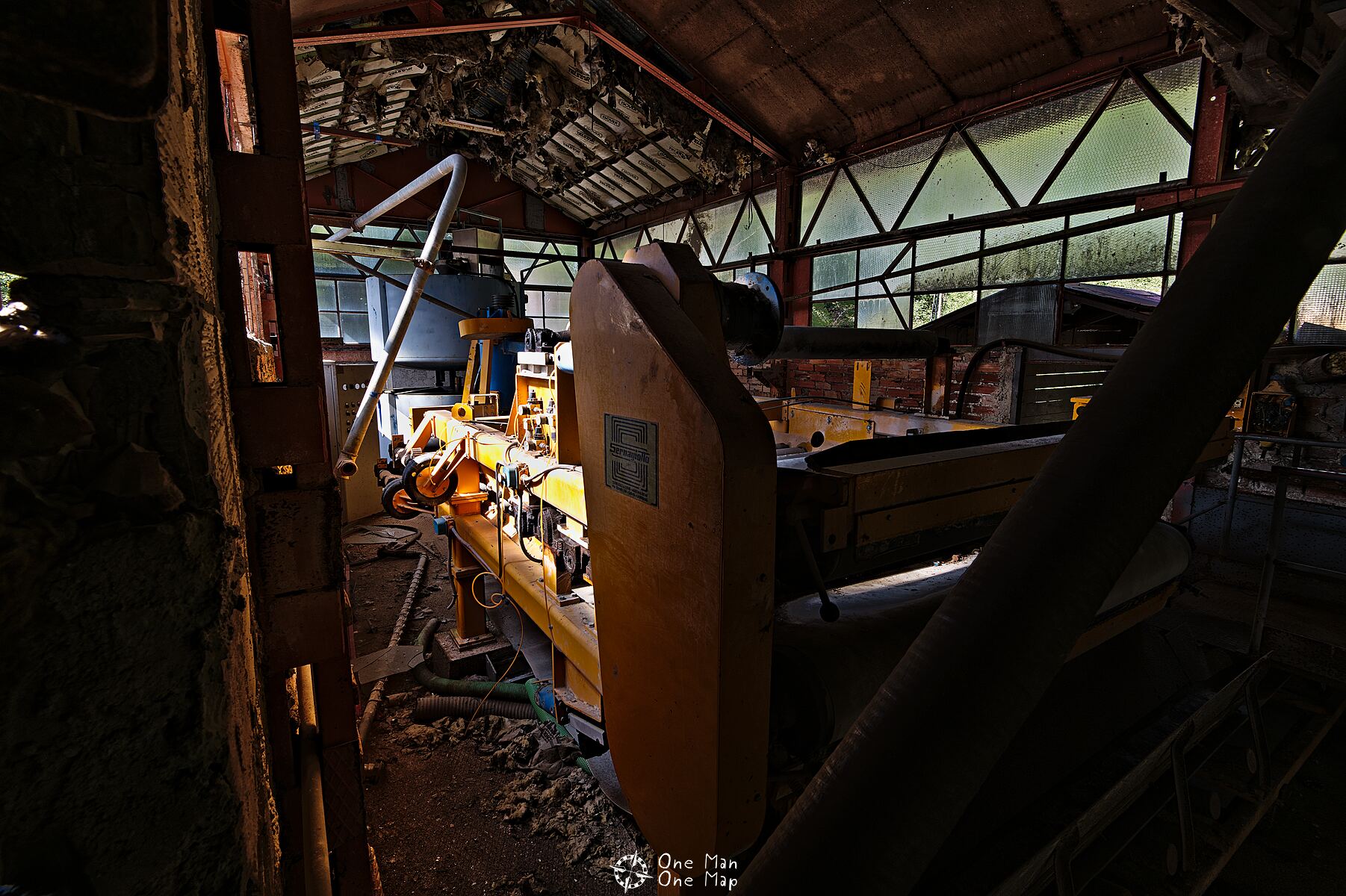
The annex building is also where the only reasonably modern machine on the whole site is located, a belt filter press made by Italian manufacturer SernaGiotto. One of the raw materials was probably dried with it. Why hasn’t it been dismantled? It must have been worth something?
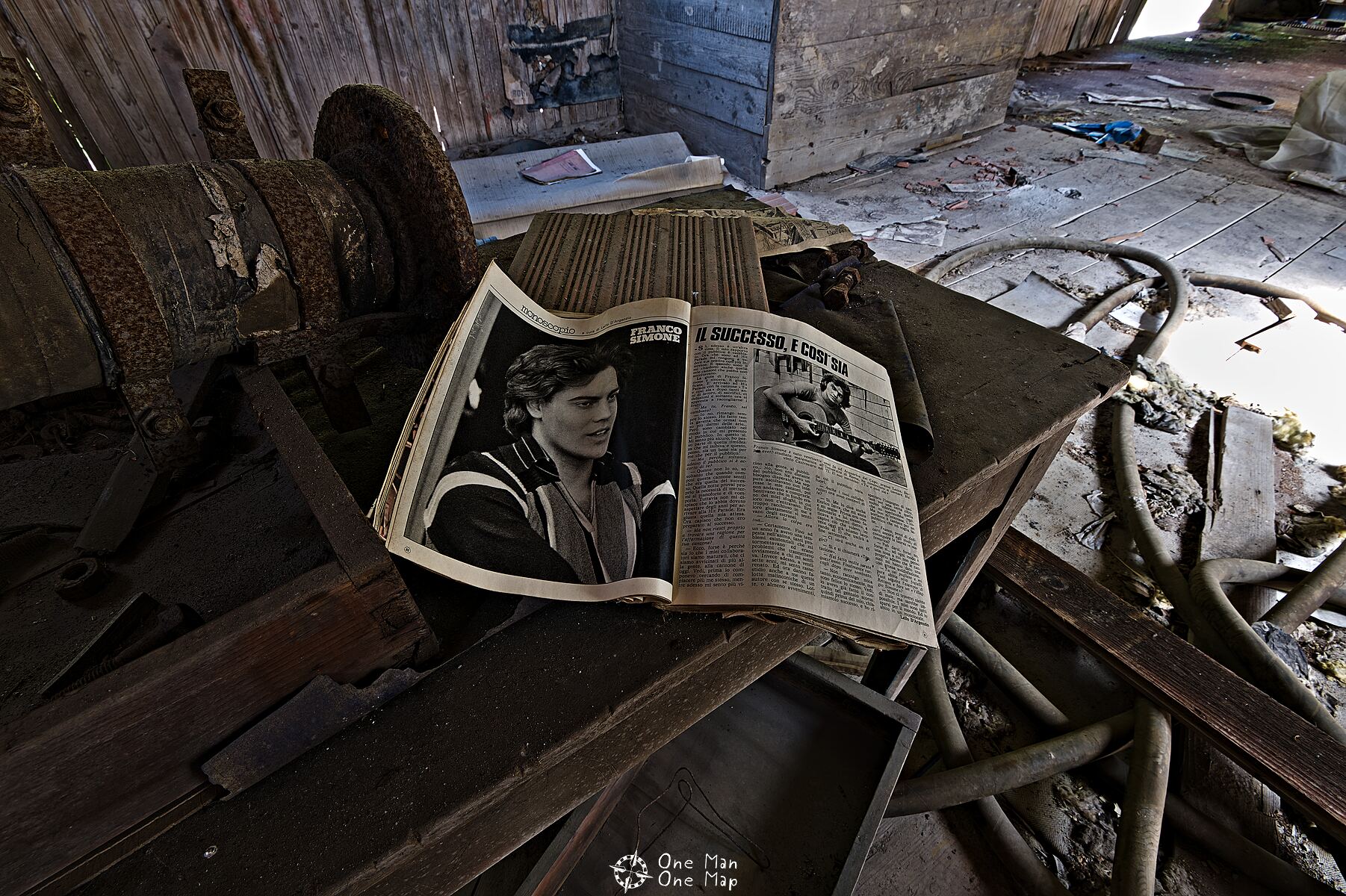
We continue on the first floor of the main building. If you look closely, you can see the many large and small holes in the ground. It consists of very thin steel plates, which were probably already no longer completely flawless before the closure…
One half of the floor is almost empty, the other is packed with machinery of all kinds. It is almost impossible to decipher their former function and the tangle of cables.
Some machines have three or four pipes running in from different floors – but what flowed in which direction?
Okay, why not just add *more* pipes? Maybe also some that go to the annex building?
I give up… 😉
The old panes of glass together with the green and blue paint of the machines and the rust create a very spooky scenery.
It probably all looked very different when the plant was still in operation. There was probably artificial lighting, clean machines, white walls and everything flashed and shone. I hope so, anyway…
The electrical wiring – or what is left of it – is also nice to look at. It’s rare to see such beautifully rusted surfaces!
After a peek into one of the larger tri-float pools, we head to the ground floor.
Of course this is the oldest part and where everything looks the worst. The walls certainly haven’t aged so much just in the last 20 years…
Here are also some of the silos from which the raw materials were then loaded onto trucks. Some of them still have material inside, so don’t stand underneath, always at the side!
Conclusion: A huge Lost Place with many unusual motifs, and not without its dangerss The eight hours I spent here were by no means enough.
This post was written by Simon for One Man, One Map. The original can be found here. All rights reserved.